The Shoe

This past year I decided to take an Introduction to Ceramics course, knowing close to nothing about the glassware. I have always known I had some artistic abilities, but this was mostly 2D. Drawing, painting, and coloring were really the only practices in my area of expertise. Then again, why not try something new. Throughout the semester I discovered a new interest, even submitting one of my pieces into a competition. The project was to create a shoe through realism or idealism. The realistic shoe would perfectly convey all aspects of a real shoe, and the idealistic shoe would resemble something abstract, at least not typical of a shoe. I began creating a navy starred Golden Goose, but it ended up being more idealistic than I ever expected. I named it “Looking Down at the Stars” writing: “Almost every quote ever made about stars says either ‘look up at the stars’ or ‘reach for the stars,’ but what if we don’t need to be in the sky to be with the stars? What if all the stars we need in our lives are already all around us? Sometimes this isn’t always the easiest to realize, but maybe looking down at the stars can remind us we are all stars. Never forget, sometimes the prettiest stars are the ones we need to look down to see.” This was the written entry I submitted to the Scholastic Art and Writing Awards and ended up winning a Silver Key.
The Process
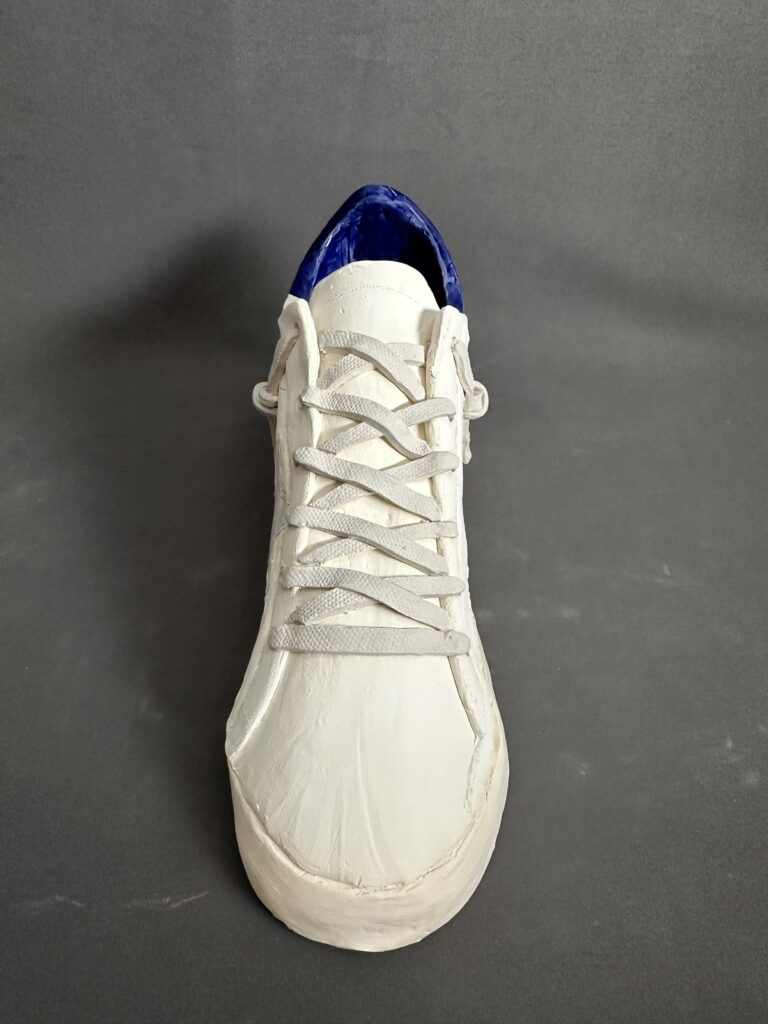
As for the process, there were various steps necessary to create such a lifelike shoe. I first had to roll the slabs of clay thin enough to avoid explosion in the kiln but thick enough to maintain shape. After cutting the shape, I attached each side to build up the shoe.When it was at the leatherhard stage, when it was sturdy enough to be carved, I then added the necessary detail including the star, the sole, the tongue, and the laces. For the laces I rolled very thin slabs and pressed them onto a canvas to add the cloth texture. To attach anything you must scratch and use slip (clay and water), ensuring everything stays in place. I added the final details and then let it dry. If water is trapped, it may explode in the kiln, so the piece must dry to the bone-dry stage before firing. This first firing is called the bisque firing producing bisqueware. The kiln heats up to 2000 degrees and takes 24 hours. The clay now becomes stone and vitrified. After using both underglaze, glaze, and oil paint to convey different materials in the shoe, it is put into a second firing. This is called the glaze firing and the piece becomes glazeware. There can be up to two firings and the glaze is now solidified on the surface. This entire process shows how a lump of clay can turn into an award winning ceramic shoe! Materials truly have endless capabilities.